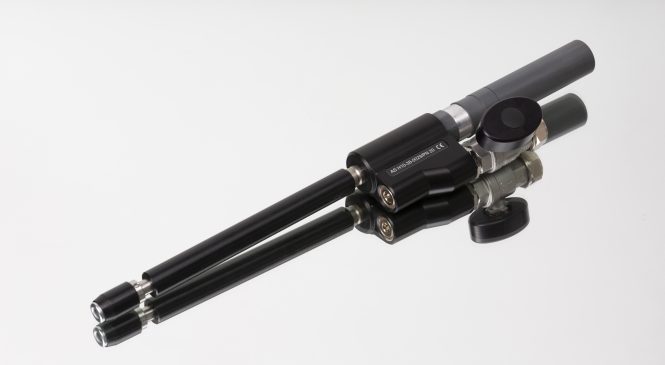
Modernized AS H 32 and AS H 38 yarn suction devices
Manual lever now even more ergonomic
Finer adjustment of the yarn suction force, lower compressed air consumption for the same yarn tension, smooth, ergonomic compressed-air valve – all promises fulfilled by the modernized AS H 32 and AS H 38 yarn suction devices.
Also known as hand injectors, these yarn suction devices are standard components of all spinning positions.
The AS H 32- and AS H 38-series high-performance hand injectors are superior to those of other manufacturers, above all as a result of their lower compressed air consumption for the same yarn tension. This is made possible due to the higher yarn suction forces, particularly in the case of the AS H 38 series. In addition to this, string-up without ‘ramp-up’ is possible in certain applications. Also new is a smoother,